- Overview
- Detailed Photos
- TDS Sheet
- Product Description
- Physical Properties
- Application
- Plastic Product Molding Method
Basic Info.
Product Description
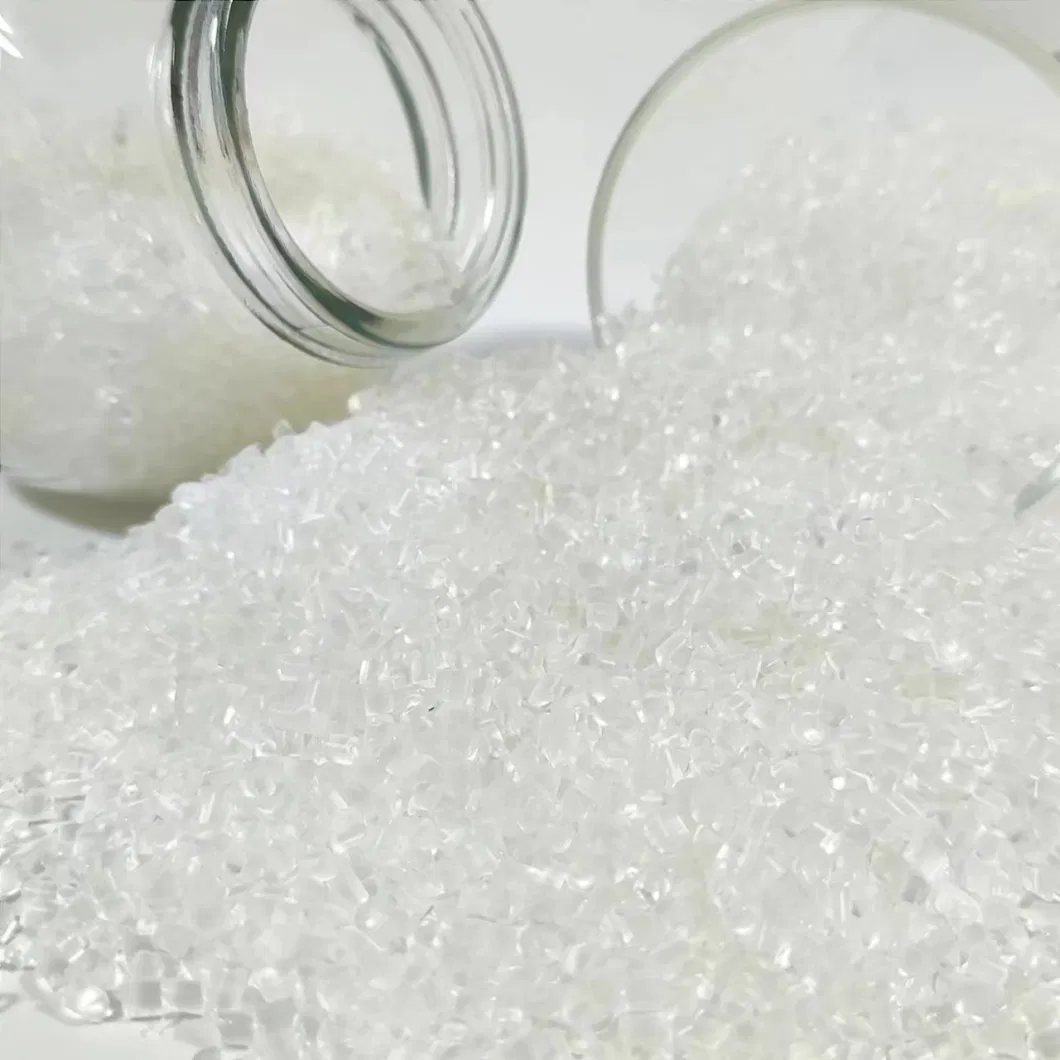
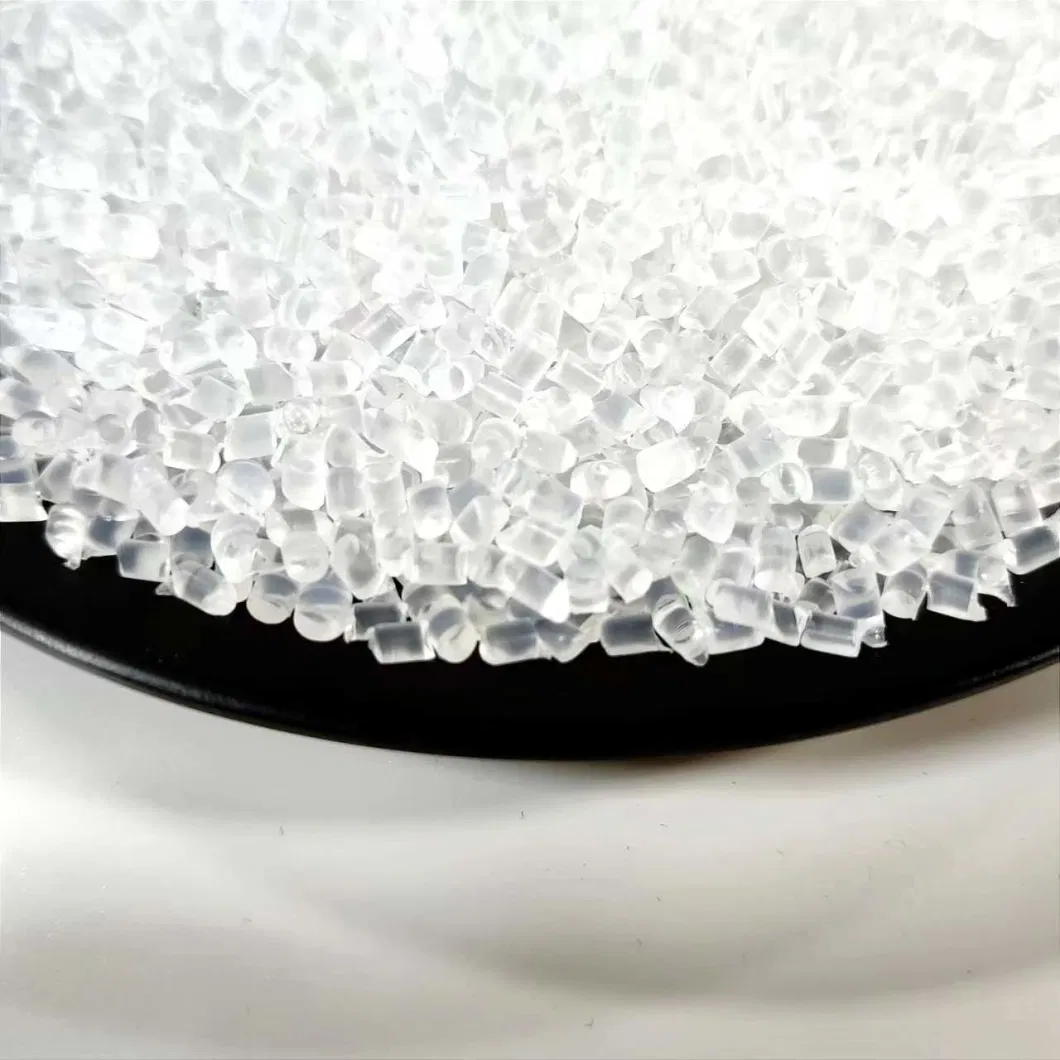
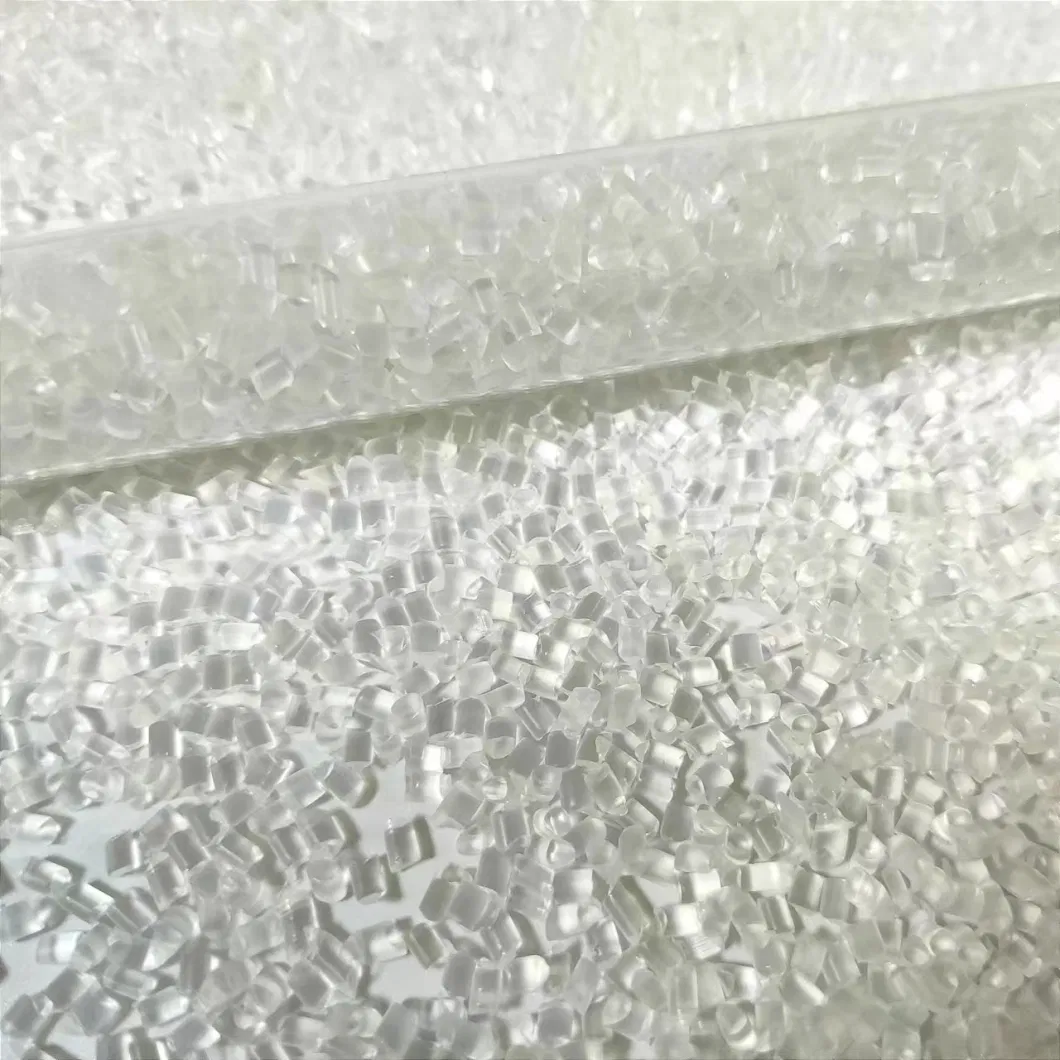
TYPICAL PROPERTIES | CONDITION | STANDARD | UNIT | VALUE |
PHYSICAL PROPERTIES | ||||
Density | ISO 1183 | [g/cm³] | 1.05 | |
Moisture absorption | T=23°C / 50%RH | ISO 62 | [%] | 0.5 |
Mold shrinkage parallel | long. | ISO 294 | [%] | 1.0 |
Mold shrinkage transverse | trans. | ISO 294 | [%] | 1.3 |
RHEOLOGICAL | ||||
Viscosity number | ISO307 | [ml/g] | 2.4 | |
MECHANICAL PROPERTIES | ||||
Tensile modulus | 1 mm/min | ISO 527 | [MPa] | 1600 |
Tensile stress at break | 50 mm/min | ISO 527 | [MPa] | 60 |
Tensile strain at break | 50mm/min | ISO 527 | [%] | 200 |
Flexural strength | 2 mm/min | ISO 178 | [MPa] | 60 |
Flexural modulus | 2 mm/min | ISO 178 | [MPa] | 1200 |
Charpy notched | +23 °C | ISO 180/1A | [kJ/m²] | 10 |
Charpy notched | - 30 °C | ISO 180/1A | [kJ/m²] | 9 |
Shore hardness(D) | ISO 868 | 75 | ||
THERMAL PROPERTIES | ||||
Heat Deflection Temperature | 0.45MPa | ISO 75 | [°C] | 155 |
Melting point | DSC | ISO 11357 | [°C] | 202 |
BURNING BEHAVIOUR | ||||
Flammability(UL94) | 0,8 mm | ISO 1210 | [Class] | HB |
Burning rate (FMVSS) | FMVSS 302 | [mm/min] |
PA1010 is made of pure green plant castor seed as raw material. Is a translucent, light and hard, bright surface of crystalline white or yellowish particles, relative density and water absorption than PA6, PA66 lower, higher than 100ºC, long-term contact with oxygen will gradually appear yellowish brown, while mechanical strength decline.
Widely used in automobile, instrument, brush making, shipbuilding, printing and dyeing, textile, railway, mining, oil, household appliances and other fields.
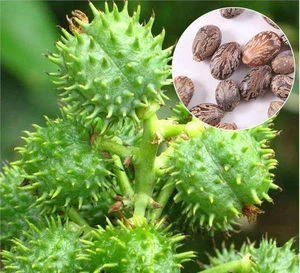
Polyamide 1010 (PA1010) is a translucent, light and hard, bright surface crystalline white or slightly yellow particles, relative density and water absorption than PA6, PA66 lower, high mechanical strength, impact toughness, wear resistance and self-lubrication good, has good sound attenuation; Good chemical resistance, non-toxic, insoluble in hydrocarbons, esters and low alcohols, concentrated sulfuric acid; Resistance to mold, bacteria and insects, with good electrical insulation; The melt has good fluidity and is easy to form, but the melt temperature range is narrow, and it is easy to be oxidizing and degraded. When it is higher than 100ºC, it will gradually show yellowish brown in contact with oxygen for a long time, and its mechanical strength will decrease.
High mechanical strength | Good impact toughness |
Wear resistance and self-lubrication | Good noise reduction |
Good oil resistance | Alkali resistance |
Chemical resistance | Insoluble in hydrocarbons |
Esters and lower alcohols | Resistant to mold |
Bacteria and Moth-eaten | Good electrical insulation |
Good melt fluidity, easy to form |
Widely used in automobile, instrument, brush making, shipbuilding, printing and dyeing, textile, railway, mining, oil, household appliances and other fields.
Building Material Industry | Marble Slab , Abrasive Brush |
Automotive Industry | Oil Tube |
Petroleum Industry | High Pressure Tube |
New Energy Source Industry | Solar Energy, Power Generation |
Electronics&Electrical Industry | 5G Communication |
Smart Wearable | Shoe Material, Shoe Arch |
Aerospace | UAV(Unmanned Aerial Vehicle) |
Consumption Industry | Wiring Harness |
Personal Articles Industry | Toothbrush |
Long carbon chain nylon has the characteristics of corrosion resistance, pressure resistance, oil resistance, cold resistance, small expansion coefficient of fuel and so on. It is an ideal material for the manufacture of automobile tubing. 60-70% of long carbon chain nylon in developed countries is used in the production of automotive hoses, such as brake tubes, pipelines, clutch hoses, etc. Long carbon chain nylon can also be used for silencing gears, bearings, thrust pads, seismic components, wipers and so on.
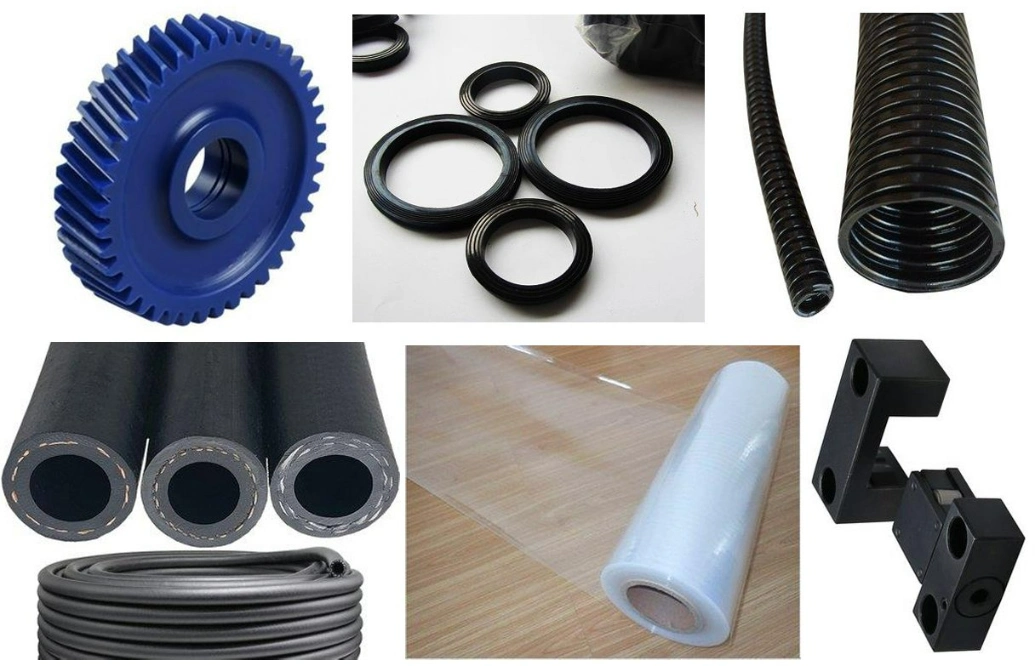
(For Reference Only)
PA1010 raw materials should be dried in the oven at about 90ºC before processing. Molding products can be processed by Injection Molding, Extrusion Blow Molding and Spraying.
(1) Temperature of extrusion cylinder: the feeding section is about 160 ° C, the homogenizing section is about 215 ° C, and the molding mold is 180~190 ° C.
(2) When injection molding, the barrel temperature is 190~230 ° C, the nozzle temperature is about 205 ° C, the mold temperature is about 30 ° C, and the injection pressure is about 110MPa.
(3) After forming the product, heat it with oil or water bath (temperature about 95ºC) for 4h.
(4) When powder spraying, the raw materials should be screened with 80 mesh screens, the powder should be heated 50~60 ° C, the pre-sprayed metal parts should be preheated to 245~255 ° C, and the flame spraying method should be used (0.2~0.25MPa CO2 gas conveying powder, acetylene pressure is 0.05MPa, oxygen pressure is 0.2~0.4MPa).